
stl came in fine and matched what the customer had. So it sees the 12 as the value and the import doesn't know or care what it is but as soon as I changed my import option to mm the. The customer exported in mm and I imported in inch. I opened a customer model and it looked correct until I made a measurement and it was 12" the real measurement was 0.473 or 12mm.
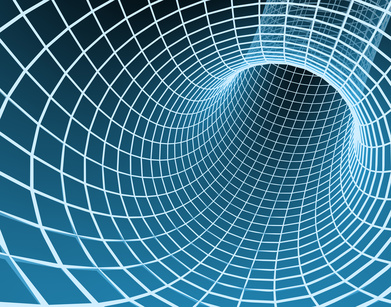
stl file (inch or mm) when opening the file and change it in your options to match before opening it to keep it at the correct values. Make sure you know what your units are of the. This next comment doesn't really have anything to do with how the Mesh Enabler works other than how you import then use the Enabler: You're not going to have a fun and easy time dealing with this one.Seems to work fine now after Rocky fixed it up. Your best bet, IF you could even get it to convert, would be to start deleting large areas that can be handled by a single surface and then replacing as many polygons as possible with new surface patches, then derive out the new patches and make your own model out of them. It can be done, but you'll require just ridiculous amounts of RAM and processor cycles with all those facets, and you will NOT be able to do anything really useful with it. You'll have to have a true beast of a computer to actually handle converting the mesh with Mesh Enabler. I hate to say it, but I think you've got about as much out of that as you can manage. The results that it gives will be cosmetic, more than functional, like you'd get from Inventor. It's a completely different way to model, as compared to a solid modeler like Inventor. When you're modeling in the kind of software that was used to create that, you create complex shapes by using lots of small triangles or quads to form surfaces, which are then shaded and rendered. The problem with that model is the polygon density.
